The analysis of mechanical loads on cables in energy chain systems is crucial to ensure the reliable and long-lasting operation of machinery and equipment. Energy chain systems, also known as drag chain systems, are used to protect and guide cables and hoses in dynamic applications where they are subject to various mechanical stresses. Here's an analysis of the mechanical loads on cables in these systems:
Bending and Flexing: Cables within energy chains experience constant bending and flexing as the chain moves. The radius of these bends is a critical factor. Excessive bending can lead to fatigue and eventual failure of the cable conductors or insulation. Engineers must calculate and design for the minimum allowable bending radius to prevent damage.
Tensile Loads: Tensile loads occur when the energy chain is in motion and the cables within it are being pulled or pushed. It's essential to calculate the maximum tensile load on the cables to ensure they can withstand these forces without breaking or stretching.
Acceleration and Deceleration: Machinery often accelerates and decelerates, subjecting the cables to dynamic forces. Rapid changes in velocity can generate additional stress on the cables. Engineers should consider these forces when selecting and designing cable systems.
Side Loads: Energy chains may experience side loads due to misalignment or uneven motion. These side loads can lead to increased friction and wear on cables, potentially causing damage over time.
Compression Loads: In certain situations, energy chains may compress the cables inside. Engineers need to account for these compressive forces to prevent deformation or damage to the cables and their insulation.
Impact Loads: External factors such as collisions or shocks can impose impact loads on the cables. The cables and the energy chain system should be designed to absorb and dissipate these forces to prevent cable damage.
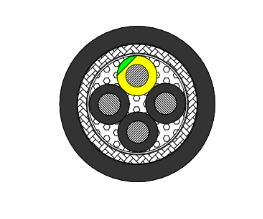
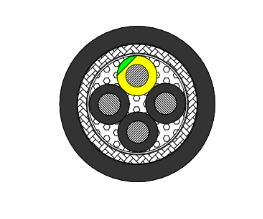
Environmental Factors: Environmental conditions, including temperature fluctuations, humidity, and exposure to chemicals or debris, can affect the mechanical properties of cables. Engineers should choose cables with appropriate jackets and insulation to withstand these conditions.
Abrasion and Wear: Cables in energy chain systems are in constant motion, and the rubbing against the chain's interior can lead to abrasion and wear. Cable selection should consider abrasion-resistant materials and designs.
Vibration: Vibrations from machinery can affect the fatigue life of cables. Proper damping and vibration-resistant cable designs can help mitigate this effect.
Cable Strain Relief: Proper strain relief mechanisms, such as cable clamps and supports within the energy chain, can distribute mechanical loads more evenly, reducing stress on the cables.
Regular Maintenance: Regular inspections and maintenance are essential to identify and address cable wear and damage promptly. Preventive measures can extend the cable's lifespan and reduce the risk of unexpected failures.
In summary, the analysis of mechanical loads on cables in energy chain systems is a complex task that requires careful consideration of various factors, including bending, tensile, compressive, and impact loads, as well as environmental conditions and vibration. Engineers must design and select cables and energy chain systems that can withstand these mechanical stresses to ensure the reliable operation of machinery and equipment.